Capabilities
We offer a complete end-to-end service tailored to your specific requirements. Whatever your needs, from specialist materials to finished components, we deliver exceptional supply chain management and customer service as standard.
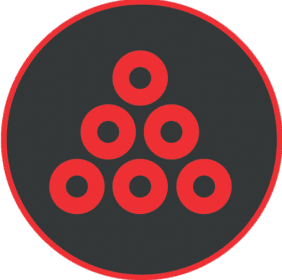
MATERIAL MANAGEMENT
Premier Hytemp is a solutions provider with the capacity and experience to manage the entire supply chain of materials and components for our customers.
Our end-to-end service offering means that we can supply forged bar from stock and forged components to order or enter into long term agreements with our customers to manage specific stock holdings, ensuring continuity of supply and agreed pricing mechanisms. We can provide components in proof machined or fully machined turnkey condition, to suit the needs of our customers.
FORGING
We have developed and refined forging routes over many years to give a specific desired microstructure and mechanical properties.
The forging temperature is critical in achieving this; in particular the final drop in temperature for Nickel Alloys, and our Metallurgists work extremely closely with the forges to ensure the highest standards are met.
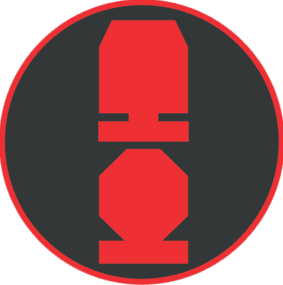
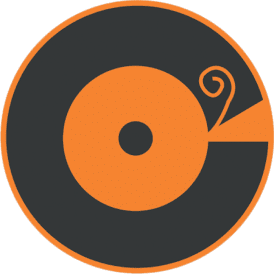
FIRST STAGE MACHINING
Premier Hytemp’s facilities in the UK and Singapore carry out the efficient saw cutting and first stage machining of bars and forgings, which is essential to the processing of metal products of all sizes. These steps make the greatest shape change in the least amount of time and are supported by our comprehensive range of saws and machines with the capacity to handle the largest materials encountered in low alloy, stainless steel and nickel alloys. We are therefore able to remove the maximum amount of raw material in the minimum time when shaping products to control processing costs and provide delivery of size and shape to agreed timescales.
HEAT TREATMENT
Premier Hytemp’s heat treatment facilities ensure that components are treated to produce the properties required in customers’ specifications.
Our in-house heat treatment system with multiple furnaces provides a full range of normalizing, hardening, annealing and tempering of alloy and stainless steels. It has a weight capacity of 10 tons, size capacity of 212 X 96 X 90 inches and a temperature range up to 1,370 degrees Centigrade. Our heat treatment system has both water and polymer quenching ability and if required, oil quench can be performed.
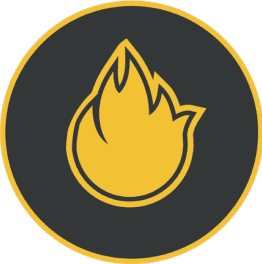
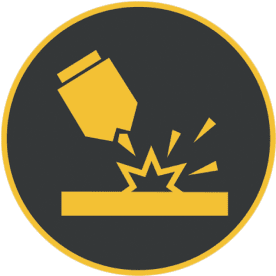
CLADDING
Premier Hytemp provides a full turnkey package of corrosion-resistant cladding and weld overlay solutions.
These services are particularly relevant for components which are deployed in harsh and corrosive environments, including specialist subsea equipment, pipes, valves and forged fittings. Vulnerable surfaces are protected by cladding them with the appropriate long-lasting alloy to provide the base materials with corrosion resistant properties. This approach can offer both cost savings and reductions in lead times for products.
FINISHED MACHINING
Premier Hytemp provides finish-machined products to customers’ specifications from its facilities in the UK and Singapore.
Finish machined products are manufactured using raw and heat-treated material from our comprehensive bar stock inventory or your supplied material. Our equipment, processes and highly skilled people guarantee the accurate, timely and repeatable machining of components to customer specifications across turning, milling and boring operations. Accuracy and reliability is achieved across the spectrum, from individual pieces to batch quantities of components.
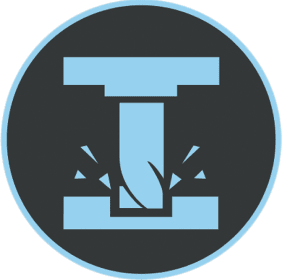
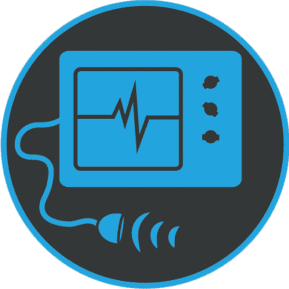
NON DESTRUCTIVE TESTING (NDT)
Premier Hytemp can perform the full range of non destructive testing. Trained technicians are qualified to perform UT examinations on forgings and finished products to PCN and ASNT standards. Using special enclosures and dark rooms Premier Hytemp are able to offer LPI and MPI on-site, streamlining the inspection process. Having access level 3 UT technicians allows Premier Hytemp to fully understand NDE specifications and define procedures to wholly comply to our customers requirements.
VALUE ADDED SERVICES
Threading Premier Hytemp is able to offer a full range of proprietary threading options through its extensive supply base at a very competitive cost and short lead times. Coating As part of Premier Hytemp’s turnkey offerings we can provide an extensive range of coating and plating options. These surface coatings protect and enhance the performance of critical components used in harsh industrial environments. Assembly Premier Hytemp has the capability to offer equipment supply by providing full assembly and pressure testing services through dedicated specialists in this field.
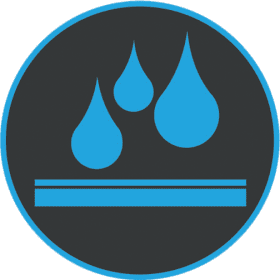